Transitioning to rapid freezing greatly reduced morning prep work! Achieving business improvements that were difficult to achieve in the past
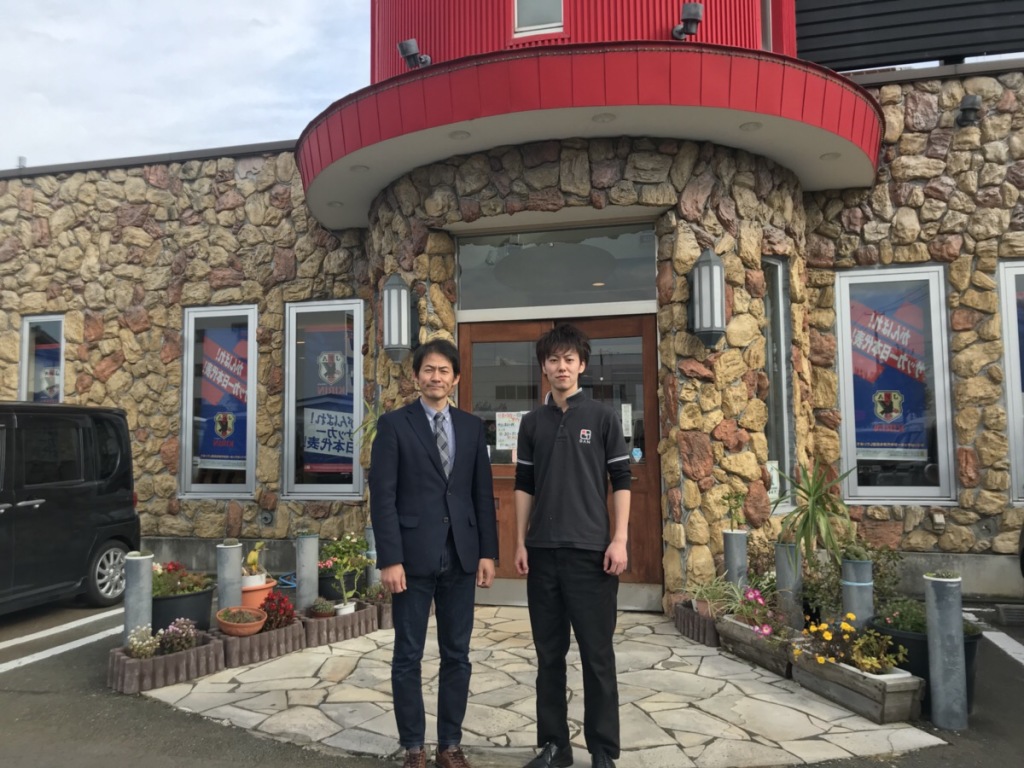
- Company Name:
- Kakashi Co., Ltd.
- Person in charge:
- President Endo
- Chef Haga
- Industry:
- Restaurants, home delivery
- Frozen items:
- Meat, semi-finished products,
- Cooked finished products, etc.
- prefectures:
- Yamagata Prefecture
- assignment
-
Due to lack of manpower, there was no time available for starting something new.
I wanted to improve work efficiency, but things were not going well.
Background of considering the introduction of rapid freezer
The theme was to improve operational efficiency in store operations and new home delivery business.
The store had been running for many years, but as times changed, we had to think of a new business model.
In order to run a business that would increase sales and make more customers happy, we searched for various ways and decided to take on new challenges such as home delivery business. This was about a year before the refrigerator was introduced.
However, the biggest obstacle in pursuing new business was the problem of a lack of human resources.
There are only a limited number of people, including head chefs, who can come up with a variety of dishes and prepare difficult dishes.
It was very difficult to think of something new while already operating existing stores.
I thought that this problem could be solved by freezing, so I consulted with Daybreak.
Effects after introducing rapid freezer
By making full use of rapid freezer during preparation, we are now able to provide dishes of stable quality at a low cost!
After actually bringing various ingredients to Daybreak and testing them, we installed rapid freezer.
It's only been a month and a half since the freezer was delivered, but it's been working very well in preparation work.
By freezing the ingredients prepared by the head chef in advance, the preparation work on the day of the meal is reduced, and even part-time staff can easily prepare and serve the food.
As a head chef, I now have more free time in the morning, and I have more than an hour each day to think about other things.
Now that anyone can easily arrange and prepare meals, it has become possible to reduce labor costs by delaying work hours and reducing the number of people on shifts.
We are able to kill two birds with one stone by reducing the cost of running our stores and freeing up time to improve our new business.
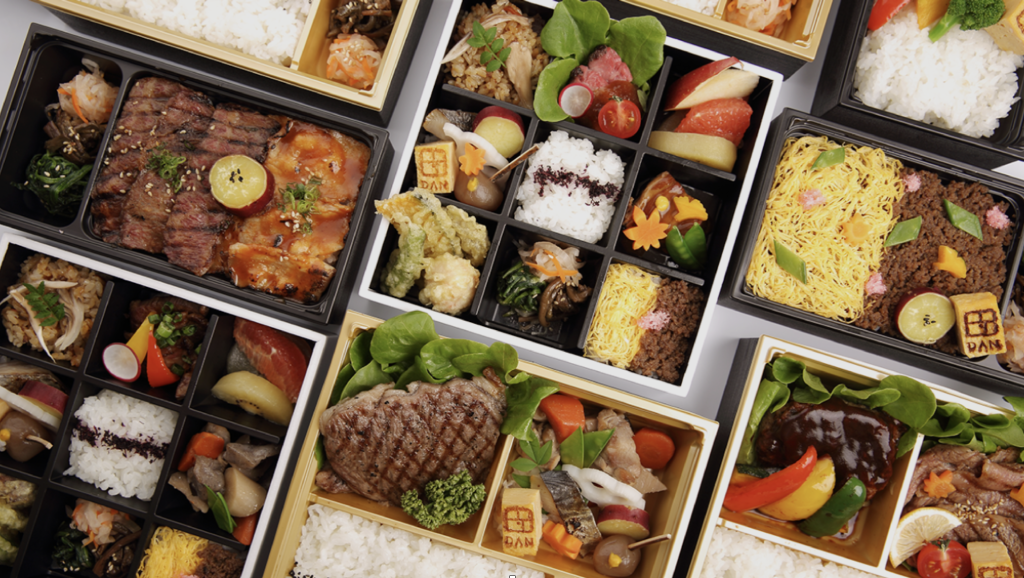
Future outlook
Thinking about ways to make better use of rapid freezer than ever before.
We will also consider ways to make better use of rapid freezer.
So that it can be used effectively for both existing store management and new business in the future,
I plan to research this for a while.
Of course it's important to come up with menus that can be frozen, but the most rewarding part is how to incorporate them into on-site operations.
I'm looking forward to the future of the company, as by making full use of rapid freezer, we can deliver even more delicious food to more customers.
We would like to continue to bring smiles to many people through Yamagata's signature scarecrow.
Why I consulted Daybreak and what was good about it
They thoroughly confirmed this through a preliminary test, and after the implementation, they suggested the optimal on-site operation!
We brought a variety of ingredients to the test room and after confirming their quality through testing, we were able to install rapid freezer.
In addition, they taught us how to freeze each type of food to achieve high-quality freezing, and together we thought about how to incorporate this into our operations.
We are able to set up an operation that allows for high-quality freezing without waste, which is very helpful.